Pioneer with intelligent 3D Digital Twin
• Research & Development
Share this article
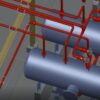
Noordgastransport (NGT) has brought natural gas from the North Sea to shore for almost 50 years. Pioneering is in the blood of the first Dutch transporter of offshore gas. The company’s activities are continuously examined and innovation is a permanent pillar in its policy. NGT plays an important role in the energy transition, by means of its reusable infrastructure at sea and the onshore station in North Groningen.
Momentarily, NGT collaborates with TP Europe to develop an ‘intelligent plant 3D Digital Twin’. “We hope that this tool enables us to transform our current installation into an ultramodern digital twin”, according to Kees Mark of NGT. We spoke to him on the plant in Uithuizen about the successful collaboration with TP Europe.
NGT
Kees Mark is Director of Operations and responsible for all NGT's operational activities both onshore and offshore. Currently, NGT transports 9 billion Nm3 of natural gas annually through a 500 km pipeline on the Dutch part of the North Sea. The impressive L10 platform is the key player of the Dutch offshore infrastructure and ensures that gas is compressed. Thereafter, the gas is brought through the pipeline to shore in Uithuizen where it is prepared for further transportation.
Kees Mark began his career at Tata Steel and Engie and made the switch to NGT in 2011. Keeping the organisation operational has many preconditions. Besides production, environment and safety of the employees, it is crucial that all operations are carried out within the laws and regulations. “We as a company are confident about our own qualities; however, it is essential to frequently test this confidence. Quality, health and safety for our people and the environment create the basis of our business operations. We test our systems annually and investigate how we can improve our processes and techniques”, says Kees Mark.
Collaboration with TP Europe
In 2015, TP Europe initiated a “Leak Detection and Repair” program that is set up in accordance with the environmental monitor 15: March, 2004.
Kees continues: “Together with TP Europe, we developed a measurement protocol to demonstrate that we operate according to the laws and regulations, and thereby create a safe work environment for our employees. With the use of this advanced measuring equipment of TP Europe, we can identify detailed emissions and possible leakages, which without this system would not be easily detected. Due to this, we are capable of executing maintenance to the system with more proactivity and accurate goal orientation. We do this by combining our Infor database to the Asset Integrity management software of TP Europe, ATLAS.”
Early this year, NGT started to make its data more intellectual and to implement it into their maintenance, environment and engineering departments. A special challenge was initiated: converting the current Autocad P&ID’s from a flat 2D to an intelligent and interactive 3D environment of the plant in Uithuizen.
3D Database
NGT sees TP Europe as trendsetter within this market segment. “You come up with ideas that are literally and figurately ‘out of the box’” Kees continues. “Two aspects play a very important role here. The first aspect is the innovative ways of detecting and reporting as TP Europe has done so far: from the P&ID, measurement results and emission trends are made transparent at a detailed level. Even though NGT has always performed well within the permitted emission threshold, this has enabled us to further reduce CO2 emissions.”
“The second aspect comes from my technical background and drive to make things ‘smarter’ and apply improvements in processes. This led to a 3D scan of our entire installation being made in 2017. The objective at the time was to get a real-time and current ‘as built’ situation of the entire plant. The plant was 43 years young then and ready for an ‘eagle-eye view’. The technologies were of such a nature that this could be achieved very accurately and within a short period of time. According to the companies that offered this 3D technology at the time, it was also relatively easy to realise the innovative ideas (communication of the 3D environment with third party data).”
“The potential result made me very excited; you have the current situation of the plant, with the 3D virtual reality you can train staff, from an online environment you can make things apparent for several people at the same time and you actually have a ‘digital twin’ as they so beautifully call it. Our ideal picture became an enormous challenge. After various brainstorming sessions, finally developed a feasible Plant 3D project, in which our requirements and wishes are also guaranteed: linking the NGT data from Infor to LDAR related data from TP Europe’s ATLAS software".
Eureka!
“This gave us the Eureka feeling! How amazing would it be if a report could be executed directly from an NGT 3D environment. In other words, a visualisation of data. This makes it really tangible. Digitally comparing historical data also ensures that we can observes trends and anticipate them at an early stage. From this detailed visual representation we can show the authorities how proactive our maintenance and reduction programs are; NGT and TP Europe have become true partners in business.”
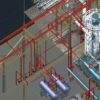
Advantages interactive and operational 3D model
“Our core business is the transport and treatment of gas and for that you simply need an installation. If we visualise this installation using virtual reality, we can make connections even more effectively. Figures or data are not very representable in themselves and instead of ‘flat data’ we need ‘smart data’. I think that a 3D environment gives a lot of insight to correctly placed data. Furthermore, it can even highlight things that normally would not stand out. It literally brings an extra dimension to our data!” Sometimes it is quite difficult to find out where the origin of the leakage lies. We then speak of a false or untraceable alarm. If we display the measurement data, originating from TP Europe, in a 3D model and supplement it with, for example, actual weather information and combine this with the data from the smart gas detectors present, this could very well ensure that even a very small leak can be detected.
Future
“Innovation starts where the horizon stops; after that further development continues”, according to Kees Mark. “We are now developing the system into a useable tool for NGT with the collaboration of TP Europe. It would be terrific if we are able to create an ultramodern digital twin from an almost 50 year old existing installation, that would be running this year!
“And what an incredible amount of additional applicable options this offers us. I am thinking, for example, of our lock-out-tag-out system, the merging of different databases that you can attach to the digital twin and providing insight into correlations between different process data. But I am also thinking of small modifications you can identify at a very early stage in the engineering phase and where you can already take into account the maintenance and the location and routing of the piping, and more of these sort of factors.”
Invest in the right business partner
“The most important thing I want to pass on to other companies that also want to develop into a ‘digital twin’ is: invest in a good scan and invest in a partner that suits you!
Choosing the right partner is essential. Build a relationship with the partner who implements your requirements, and start the development together.
For us, that is still TP Europe, a business partner that works with us on a detailed level and provides solutions.” Kees Mark’s personal innovative wish is clear; “Simply being able to display and edit the plant as a hologram from a platform, including underlying and retrievable intelligent data.
But, there are still some years to go for me, so this one will remain in my “wish book” for now.